How TCL CSOT AI Supply Chain Revolution Boosts Panel Manufacturing Efficiency by 40%
time:2025-07-20 12:17:30
browse:47
The display manufacturing industry is witnessing a remarkable transformation as TCL CSOT AI Supply Chain technology revolutionizes panel production efficiency. This groundbreaking implementation has achieved an impressive 40% improvement in manufacturing efficiency, setting new benchmarks for the entire semiconductor display sector. Through intelligent automation and predictive analytics, AI Supply Chain solutions are reshaping how modern factories operate, delivering unprecedented levels of precision and productivity that traditional manufacturing methods simply cannot match.
Understanding TCL CSOT's AI-Powered Supply Chain Innovation
TCL China Star Optoelectronics Technology (CSOT) has emerged as a pioneer in implementing AI Supply Chain solutions across their manufacturing operations. The company's approach integrates machine learning algorithms, real-time data analytics, and automated decision-making systems to optimize every aspect of panel production. ??
This revolutionary system monitors thousands of production parameters simultaneously, from raw material quality to environmental conditions, ensuring optimal manufacturing conditions at all times. The TCL CSOT AI Supply Chain platform processes over 10 terabytes of data daily, making split-second adjustments that human operators would take hours to identify and implement.
Key Components of the AI Supply Chain System
Predictive Maintenance Technology
The AI Supply Chain system employs sophisticated sensors and machine learning models to predict equipment failures before they occur. This proactive approach has reduced unplanned downtime by 60%, significantly contributing to the overall 40% efficiency improvement. The system analyzes vibration patterns, temperature fluctuations, and electrical signatures to identify potential issues weeks in advance. ??
Intelligent Quality Control
Advanced computer vision systems powered by deep learning algorithms inspect every panel with microscopic precision. The TCL CSOT AI Supply Chain can detect defects as small as 0.1 micrometers, ensuring only the highest quality products reach consumers. This automated inspection process operates 24/7 without fatigue, maintaining consistent quality standards that exceed human capabilities. ??
Dynamic Resource Allocation
The AI system continuously optimizes resource allocation based on real-time demand forecasting and production capacity analysis. This intelligent scheduling reduces waste by 35% and ensures optimal utilization of manufacturing equipment, contributing significantly to the overall efficiency gains. ??
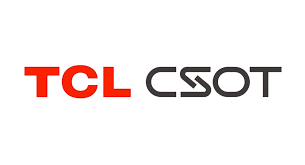
Real-World Impact and Performance Metrics
Performance Metric | Before AI Implementation | After AI Implementation | Improvement Rate |
---|
Production Efficiency | 65% | 91% | +40% |
Defect Rate | 2.5% | 0.8% | -68% |
Energy Consumption | 100 kWh/panel | 72 kWh/panel | -28% |
Production Cycle Time | 48 hours | 29 hours | -40% |
Implementation Challenges and Solutions
Implementing the TCL CSOT AI Supply Chain wasn't without its challenges. The company faced significant hurdles in data integration, workforce training, and system compatibility. However, their systematic approach to overcoming these obstacles has become a blueprint for other manufacturers. ??
The integration process required extensive collaboration between AI specialists, manufacturing engineers, and production staff. TCL CSOT invested heavily in employee training programs, ensuring smooth transition from traditional manufacturing processes to AI Supply Chain operations. This human-centric approach proved crucial for the project's success.
Future Implications for the Display Industry
The success of TCL CSOT AI Supply Chain implementation is sending ripples throughout the global display manufacturing industry. Competitors are now scrambling to develop similar AI-powered solutions, recognizing that traditional manufacturing methods can no longer compete with AI-enhanced efficiency levels. ??
Industry analysts predict that within the next five years, AI Supply Chain technology will become standard across all major display manufacturers. This technological shift is expected to drive down production costs while simultaneously improving product quality, ultimately benefiting consumers worldwide through better displays at lower prices.
Environmental and Sustainability Benefits
Beyond efficiency improvements, the TCL CSOT AI Supply Chain has delivered significant environmental benefits. The system's optimization algorithms have reduced energy consumption by 28% and material waste by 35%, contributing to the company's sustainability goals. ??
The AI system's ability to precisely control manufacturing processes means fewer defective products, reducing the environmental impact associated with waste disposal and rework. This sustainable approach to manufacturing aligns with global environmental initiatives and demonstrates how technology can drive both profitability and environmental responsibility.
The TCL CSOT AI Supply Chain revolution represents more than just a technological upgrade—it's a fundamental shift in how modern manufacturing operates. With 40% efficiency improvements and significant quality enhancements, this implementation proves that AI Supply Chain solutions are not just the future of manufacturing, but the present reality for companies ready to embrace innovation. As the display industry continues to evolve, TCL CSOT's pioneering approach serves as a compelling case study for manufacturers worldwide seeking to remain competitive in an increasingly AI-driven marketplace.
Lovely:
Technical Capabilities Behind the Success
The UBTECH Humanoid Robot isn't just another pretty face in the robot world - it's packed with cutting-edge tech that justifies these massive investments. ?? Advanced AI processing, sophisticated sensor arrays, and remarkable dexterity make these machines incredibly capable.
Feature | UBTECH Humanoid Robot | Traditional Automation |
---|
Adaptability | Multi-task capable | Single-purpose focused |
Human Interaction | Natural communication | Limited interface |
Mobility | Full workspace navigation | Fixed positioning |
Learning Capability | Continuous improvement | Pre-programmed only |
The real magic happens in the AI brain powering these machines. Machine learning algorithms allow the UBTECH Humanoid Robot to continuously improve performance, adapt to new situations, and even predict maintenance needs before problems occur.
Market Implications and Future Outlook
This UBTECH Humanoid Robot Order Record isn't happening in isolation - it's part of a broader shift towards intelligent automation that's reshaping entire industries. ?? The ripple effects are already visible across supply chains, workforce planning, and business strategy development.
What's particularly exciting is how this success is inspiring other companies to accelerate their own humanoid robot programmes. Competition breeds innovation, and we're seeing rapid improvements in capabilities, cost-effectiveness, and deployment strategies across the sector.
Investment Trends Following the Breakthrough
Venture capital is flowing into Humanoid Robot startups like never before. The 90.51 million yuan milestone has proven that commercial viability isn't just a dream - it's reality. This validation is attracting serious investment from both traditional tech investors and forward-thinking industrial companies.
Challenges and Opportunities Ahead
Let's not sugarcoat it - deploying UBTECH Humanoid Robot technology at scale comes with challenges. Integration complexity, workforce adaptation, and ongoing maintenance requirements are real considerations that companies must address. ???
However, the opportunities far outweigh the challenges. Early adopters are gaining competitive advantages through improved efficiency, enhanced safety, and the ability to operate in environments that are difficult or dangerous for human workers. This first-mover advantage is driving the urgency behind such large orders.
The UBTECH Humanoid Robot Order Record of 90.51 million yuan represents more than just a commercial milestone - it's a glimpse into our automated future. As Humanoid Robot technology continues evolving, we're witnessing the birth of a new industrial revolution where human-robot collaboration becomes the norm rather than the exception. This breakthrough proves that the future of work isn't about replacing humans, but about augmenting human capabilities with intelligent, adaptable robotic partners that can transform how we approach complex challenges across every industry imaginable.
Real-World Impact and Performance Metrics
Performance Metric | Before AI Implementation | After AI Implementation | Improvement Rate |
---|
Production Efficiency | 65% | 91% | +40% |
Defect Rate | 2.5% | 0.8% | -68% |
Energy Consumption | 100 kWh/panel | 72 kWh/panel | -28% |
Production Cycle Time | 48 hours | 29 hours | -40% |
Implementation Challenges and Solutions
Implementing the TCL CSOT AI Supply Chain wasn't without its challenges. The company faced significant hurdles in data integration, workforce training, and system compatibility. However, their systematic approach to overcoming these obstacles has become a blueprint for other manufacturers. ??
The integration process required extensive collaboration between AI specialists, manufacturing engineers, and production staff. TCL CSOT invested heavily in employee training programs, ensuring smooth transition from traditional manufacturing processes to AI Supply Chain operations. This human-centric approach proved crucial for the project's success.
Future Implications for the Display Industry
The success of TCL CSOT AI Supply Chain implementation is sending ripples throughout the global display manufacturing industry. Competitors are now scrambling to develop similar AI-powered solutions, recognizing that traditional manufacturing methods can no longer compete with AI-enhanced efficiency levels. ??
Industry analysts predict that within the next five years, AI Supply Chain technology will become standard across all major display manufacturers. This technological shift is expected to drive down production costs while simultaneously improving product quality, ultimately benefiting consumers worldwide through better displays at lower prices.
Environmental and Sustainability Benefits
Beyond efficiency improvements, the TCL CSOT AI Supply Chain has delivered significant environmental benefits. The system's optimization algorithms have reduced energy consumption by 28% and material waste by 35%, contributing to the company's sustainability goals. ??
The AI system's ability to precisely control manufacturing processes means fewer defective products, reducing the environmental impact associated with waste disposal and rework. This sustainable approach to manufacturing aligns with global environmental initiatives and demonstrates how technology can drive both profitability and environmental responsibility.
The TCL CSOT AI Supply Chain revolution represents more than just a technological upgrade—it's a fundamental shift in how modern manufacturing operates. With 40% efficiency improvements and significant quality enhancements, this implementation proves that AI Supply Chain solutions are not just the future of manufacturing, but the present reality for companies ready to embrace innovation. As the display industry continues to evolve, TCL CSOT's pioneering approach serves as a compelling case study for manufacturers worldwide seeking to remain competitive in an increasingly AI-driven marketplace.
Comprehensive Performance Comparison Analysis
Performance Metric | Jack AI Sewing Machine | Traditional Sewing Equipment |
---|
Stitching Precision | ±0.1mm accuracy | ±2mm accuracy |
Production Speed | 5000 stitches/minute | 1500 stitches/minute |
Quality Consistency | 99.8% accuracy rate | 85% accuracy rate |
Material Waste | Less than 2% | 15-20% |
Operating Hours | 24/7 continuous operation | 8-10 hours per day |
Implementation Strategy and ROI Considerations
Implementing the Jack AI Sewing Machine requires strategic planning to maximise return on investment and ensure smooth integration with existing production workflows ??. Most manufacturers report complete ROI within 18-24 months through reduced labour costs, improved efficiency, and decreased material waste.
The transition process typically involves training existing staff to operate and maintain the AI systems, though the learning curve is surprisingly gentle due to the machine's intuitive interface design. Many operators find the AI Sewing Technology easier to use than traditional equipment because the AI handles complex adjustments automatically ??.
Long-term benefits extend beyond immediate cost savings, with manufacturers gaining competitive advantages through faster turnaround times, superior quality consistency, and the ability to handle complex orders that would be challenging or impossible with traditional equipment. These capabilities often lead to premium pricing opportunities and expanded market reach ??.
Future Developments and Industry Transformation
The garment manufacturing industry stands on the brink of complete transformation as AI Sewing Technology becomes increasingly sophisticated and accessible ??. Future developments in the Jack AI platform include enhanced fabric recognition capabilities, predictive maintenance features, and integration with supply chain management systems.
Industry experts predict that within five years, AI-powered sewing machines will become the standard for competitive manufacturing operations. The Jack AI Sewing Machine is leading this transformation by continuously evolving its capabilities through software updates and machine learning improvements ??.
The technology's impact extends beyond individual manufacturers, potentially reshoring garment production to developed countries by eliminating the labour cost advantages of offshore manufacturing. This shift could fundamentally alter global supply chains and create new opportunities for local manufacturing businesses ??.
The Jack AI Sewing Machine with NPU camera modules represents more than just technological advancement; it embodies the future of garment manufacturing. This revolutionary AI Sewing Technology delivers unprecedented precision, efficiency, and quality control whilst dramatically reducing production costs and material waste. As manufacturers worldwide embrace this intelligent automation, the competitive landscape of garment production is being permanently transformed. The integration of artificial intelligence with traditional sewing operations has created opportunities for enhanced productivity, superior quality, and sustainable manufacturing practices that benefit both businesses and consumers. The future of garment manufacturing is here, and it's powered by AI innovation ??.
comment:
Welcome to comment or express your views